I agree with the FNG (yeah you Jon, lol). You don't need to get so elaborate with turbo collectors beyond a nice merge. In N/A applications it is more important, but making collectors like the ones below are difficult enough to make, nevermind "vortex collectors"...
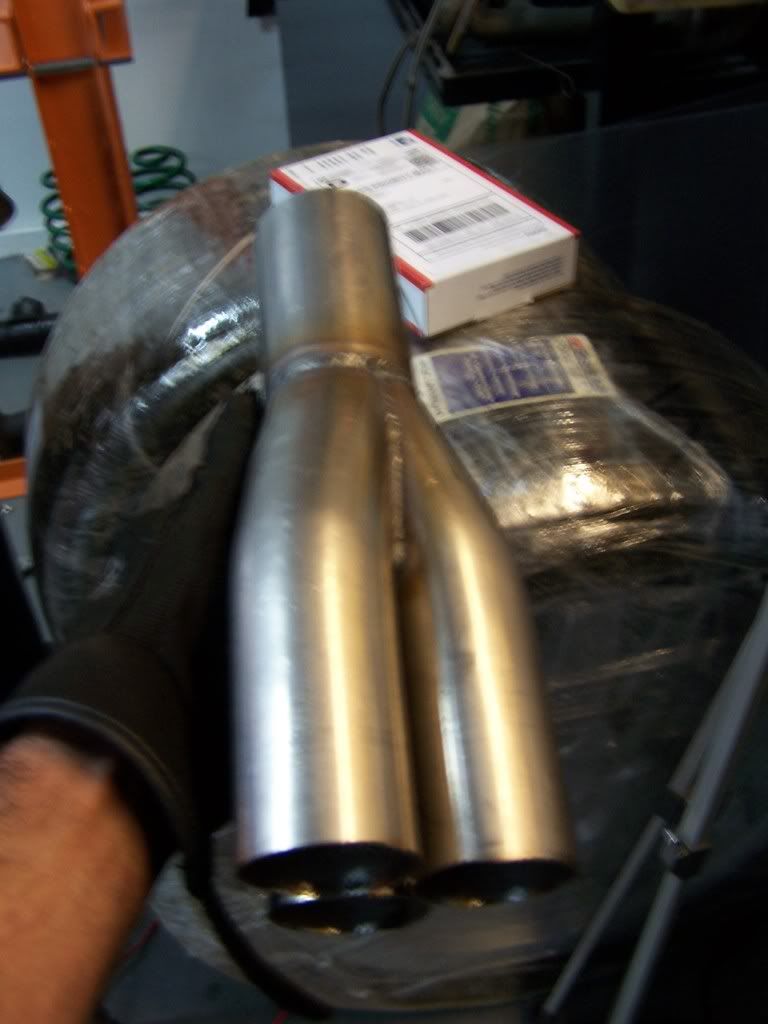
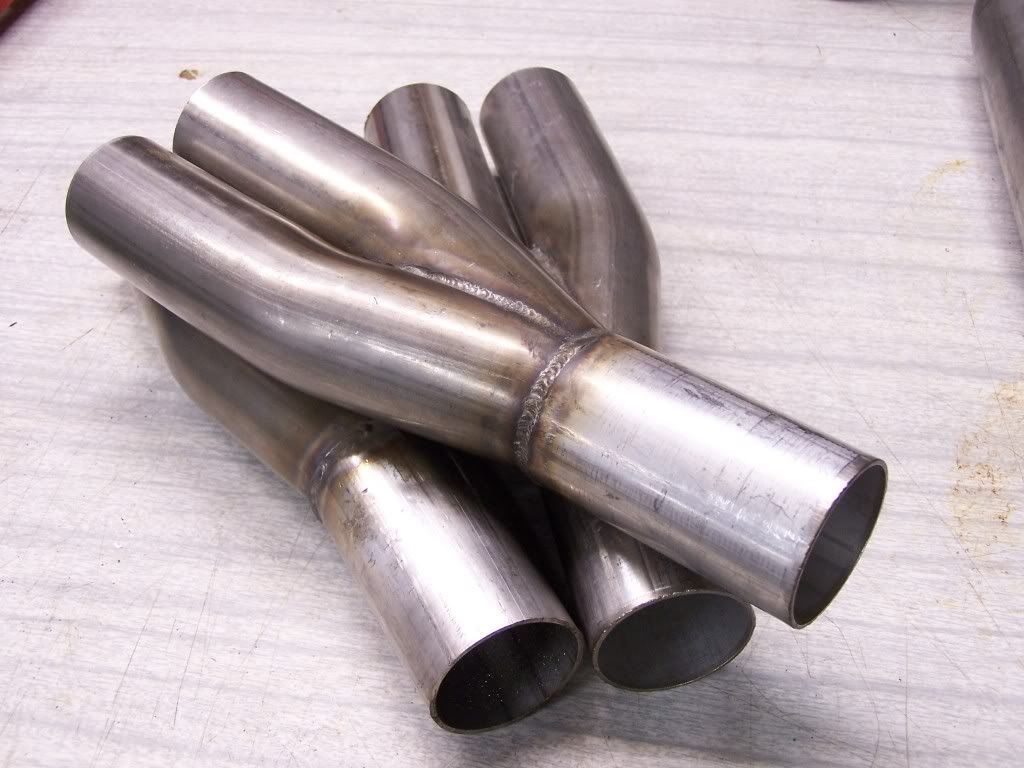
I don't like using thin walled pipe for turbo applications, they always crack unless you have extreme turbo bracing since the heat cycles will practically melt - used 14ga on a couple applications and they held with extra welding and bracing, but the sch10 will hold the weight, heat and is actually easier to weld.
I also used that Honda forum to get ideas to make a jig to produce the above collectors, but had to change things a bit since I was using 18degree bends for a Burns-style collector rather than sch10 straight piping. The 2-1's were made on the bandsaw, the 3-1 was made on a metal cutoff saw.
I will disagree, though, that collector design doesn't matter. In N/A, S/C and nitrous applications, it is VERY important. A local here with an outlaw Buick Regal (7second car) picked up several tenths by switching to a Burns collector and larger primaries.
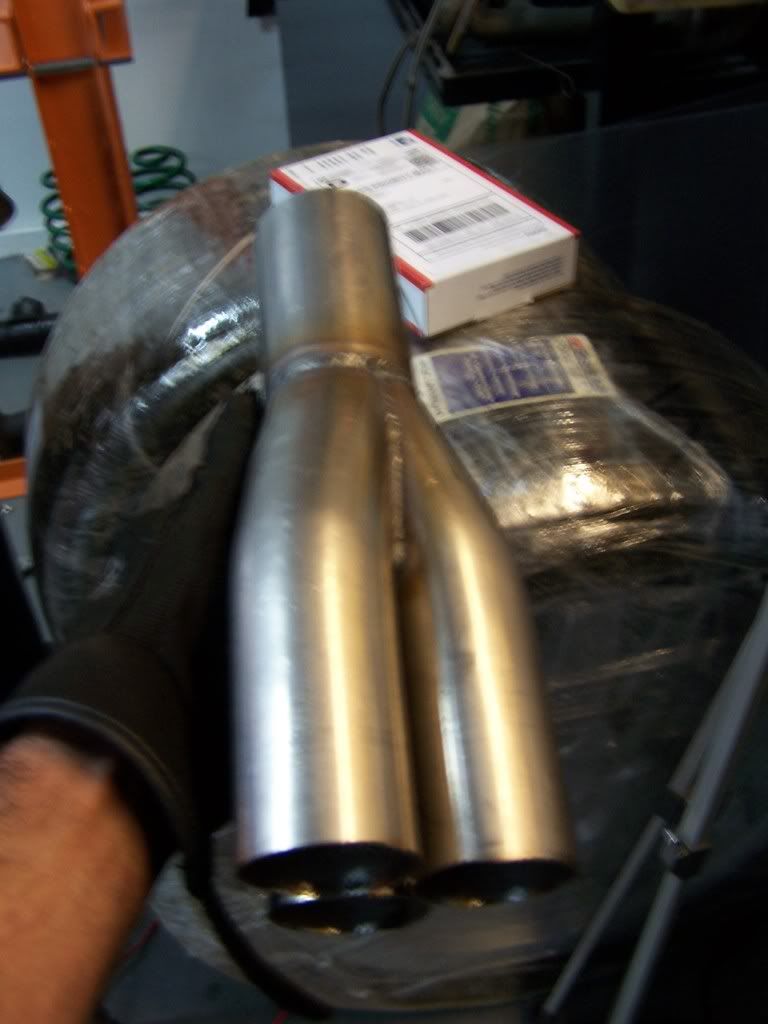
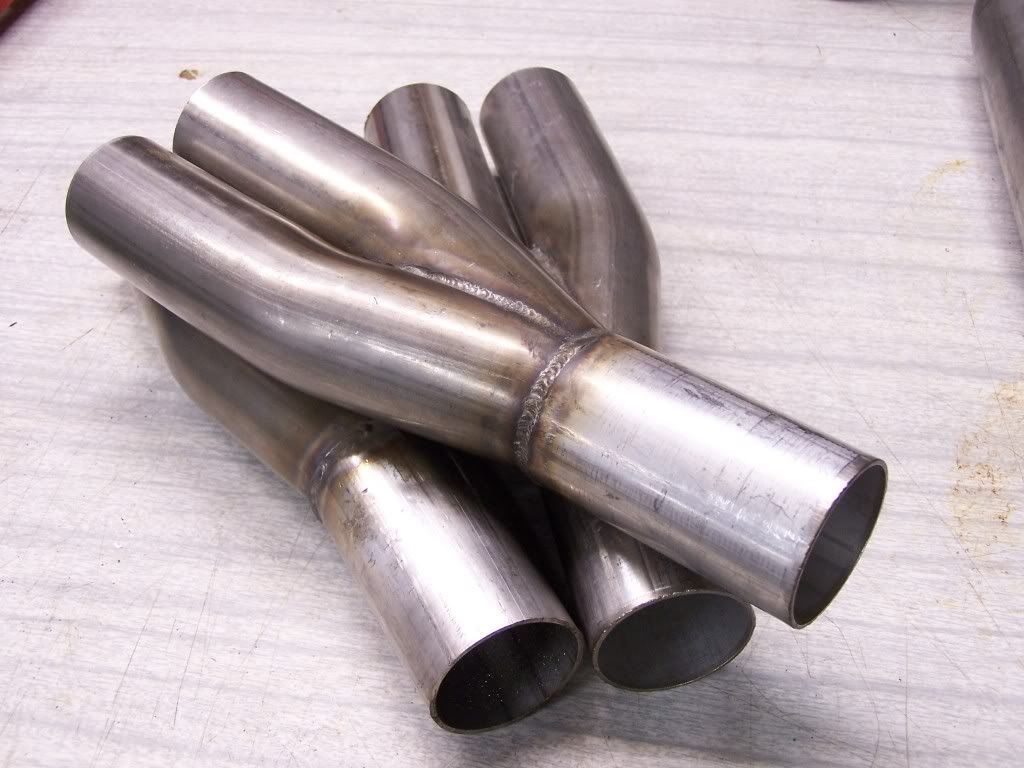
I don't like using thin walled pipe for turbo applications, they always crack unless you have extreme turbo bracing since the heat cycles will practically melt - used 14ga on a couple applications and they held with extra welding and bracing, but the sch10 will hold the weight, heat and is actually easier to weld.
I also used that Honda forum to get ideas to make a jig to produce the above collectors, but had to change things a bit since I was using 18degree bends for a Burns-style collector rather than sch10 straight piping. The 2-1's were made on the bandsaw, the 3-1 was made on a metal cutoff saw.
I will disagree, though, that collector design doesn't matter. In N/A, S/C and nitrous applications, it is VERY important. A local here with an outlaw Buick Regal (7second car) picked up several tenths by switching to a Burns collector and larger primaries.
Comment