I've been researching alot on other sites (LS1tech, turbomustangs)for this idea and I think it'll work, but wanted to know if anyone here had real life experience with this.
It's about welding normal steel pipe to a manifold. Seems the newer (ish) manifolds are made of a nice carbon steel that welds very well.
I tried a test here, and it worked well (i think ?) This was no prep, no pre-heat, no slow cooldown, no nothin'. 2" 16ga. aluminised pipe to a 3900 manifold that I cut apart. FLUX CORE MIG, you can see by the spatter.
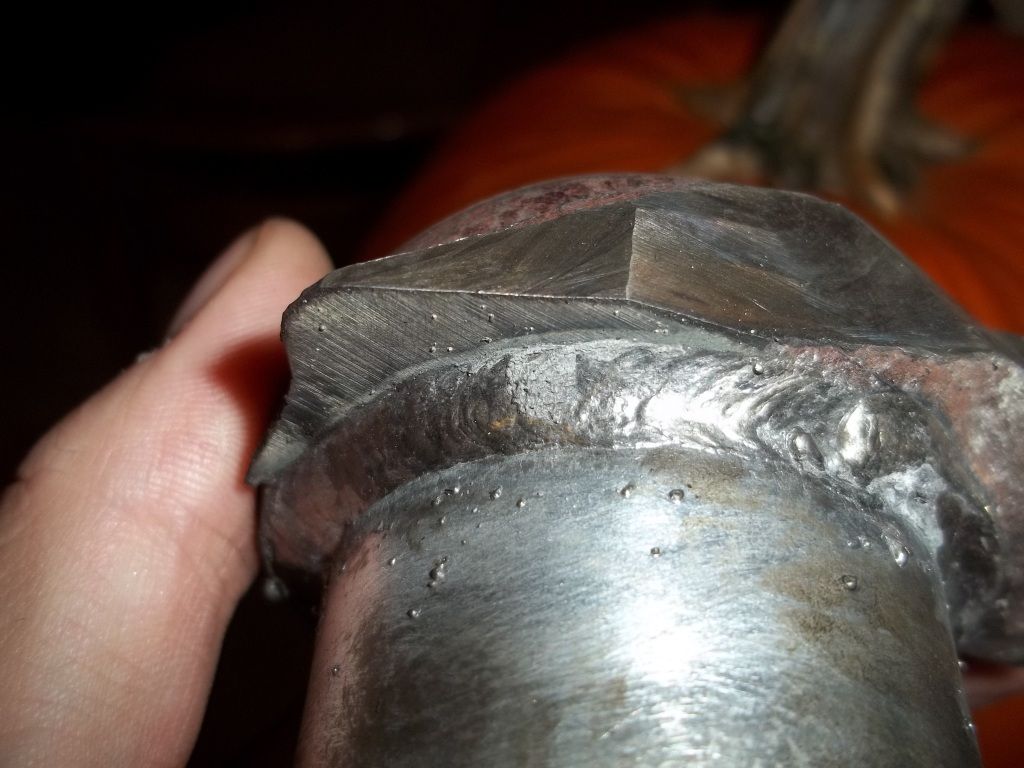
As you can see it layed a nice bead down, the welder worked well, nice puddle, not much spatter, ect. i think it would be tough as all hell. After it cooled I grabbed the biggest hammer I could and demo'd the thing and it didn't break in the weld. It tore the smaller pipe just above the weld, which is precisely what I predicted would happen..
As I build this 3900 turbo engine, and do the turbo pipes, I am starting to think I'll abandon the custom header idea and use manifolds. I may even do something super-custom for the driver's side that I have planned IF this manifold welding thing works...
I was thinking of using steam pipe SHC40 in a 2" and just welding it right to the manifold about a 100* angle right into the T4 flange about 8" away.... With just enough room for a gate, all one piece, fully welded for the pass side, then a V-band and flex heading to the pass side off the other side of the divided T4 flange.
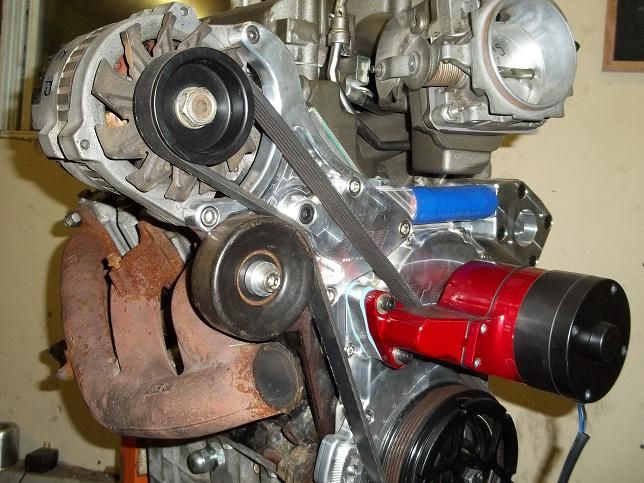
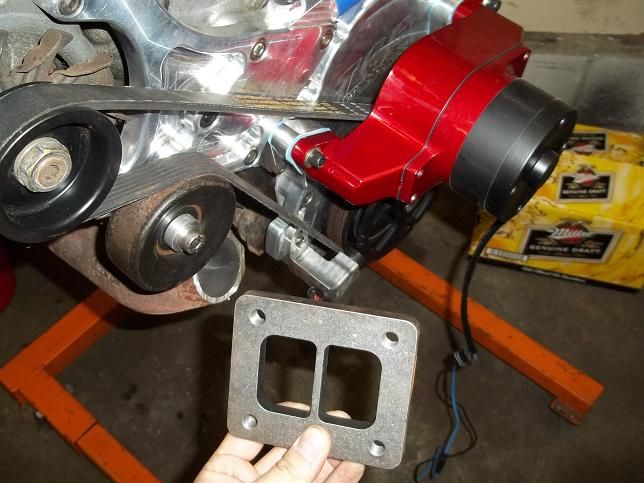
I'm thinking it would spool quick in that location... 3.5" exhaust would be going alongside the alt. then down.
It's about welding normal steel pipe to a manifold. Seems the newer (ish) manifolds are made of a nice carbon steel that welds very well.
I tried a test here, and it worked well (i think ?) This was no prep, no pre-heat, no slow cooldown, no nothin'. 2" 16ga. aluminised pipe to a 3900 manifold that I cut apart. FLUX CORE MIG, you can see by the spatter.

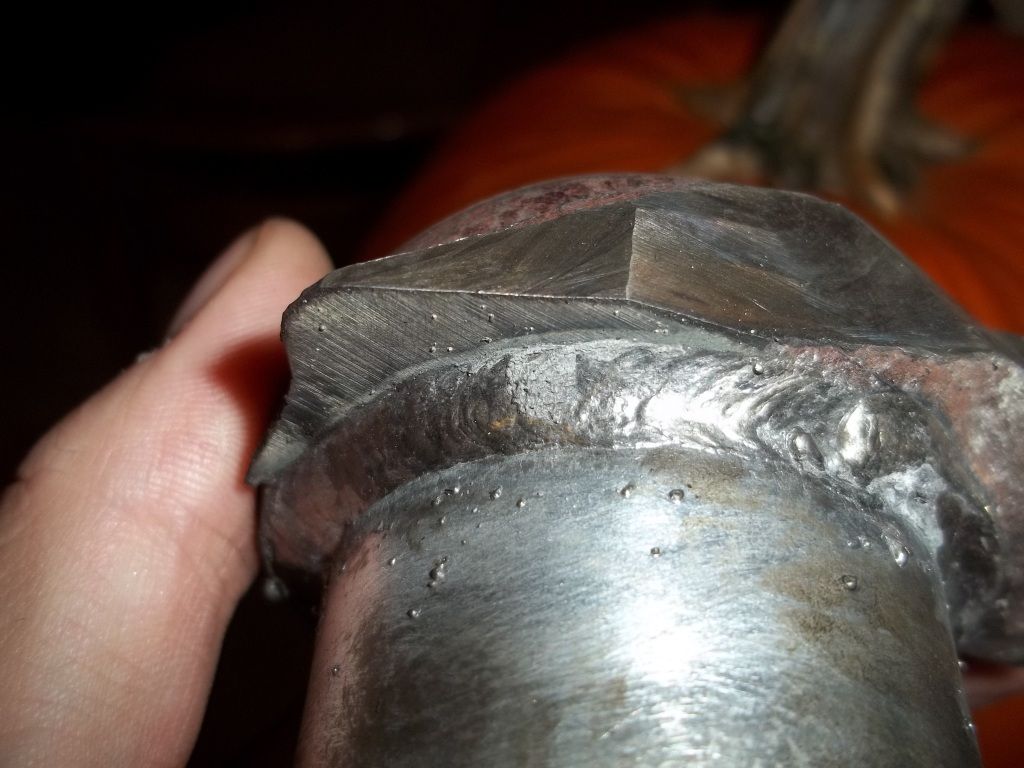
As you can see it layed a nice bead down, the welder worked well, nice puddle, not much spatter, ect. i think it would be tough as all hell. After it cooled I grabbed the biggest hammer I could and demo'd the thing and it didn't break in the weld. It tore the smaller pipe just above the weld, which is precisely what I predicted would happen..
As I build this 3900 turbo engine, and do the turbo pipes, I am starting to think I'll abandon the custom header idea and use manifolds. I may even do something super-custom for the driver's side that I have planned IF this manifold welding thing works...
I was thinking of using steam pipe SHC40 in a 2" and just welding it right to the manifold about a 100* angle right into the T4 flange about 8" away.... With just enough room for a gate, all one piece, fully welded for the pass side, then a V-band and flex heading to the pass side off the other side of the divided T4 flange.
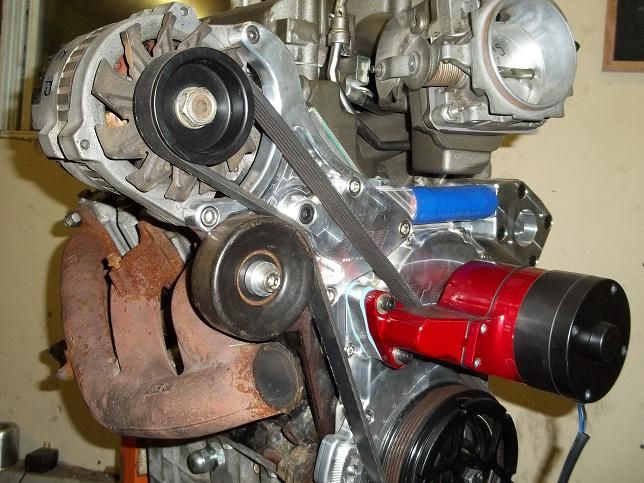
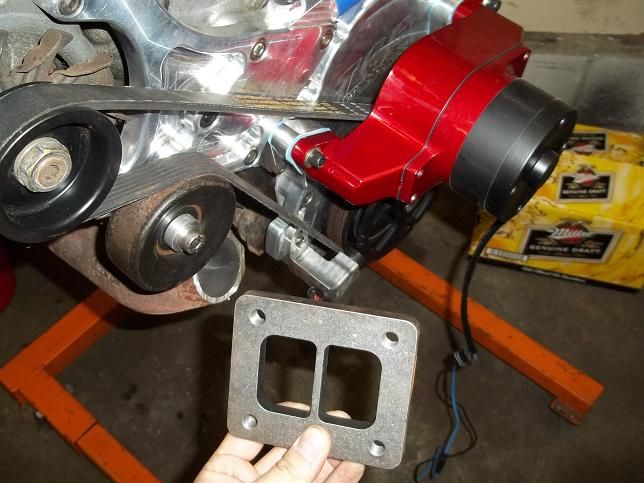
I'm thinking it would spool quick in that location... 3.5" exhaust would be going alongside the alt. then down.
Comment